The Surprising Connection Between Crafting Pro Baseball Gloves and Fine Guitars
News & Articles
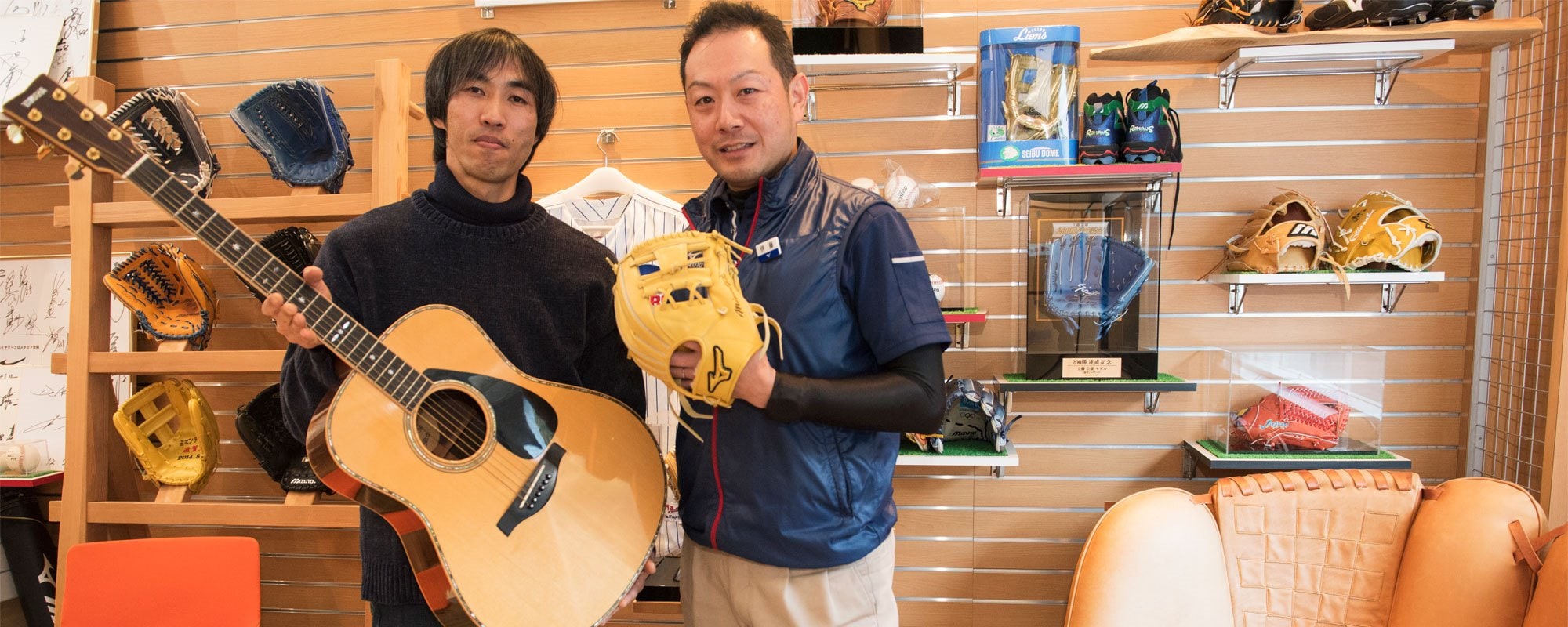
The Surprising Connection Between Crafting Pro Baseball Gloves and Fine Guitars
Guitars and baseball gloves are from different worlds, but the philosophies of the craftsmen who make them have many points in common.
Tadahiro Suzuki of Yamaha oversees the production of high-end Japanese-made guitars, including acoustic, classical and electric models. As manager of prototype development at Mizuno, craftsman Norifumi Ito is responsible for the manufacturing of thousands of baseball gloves, including many for Major League Baseball players. As two craftsman who have supported players all over the world, Sukuki and Ito recently sat down to discuss the commonalities between making guitars and baseball gloves, including a refined selection of materials and a focus on the end user experience.
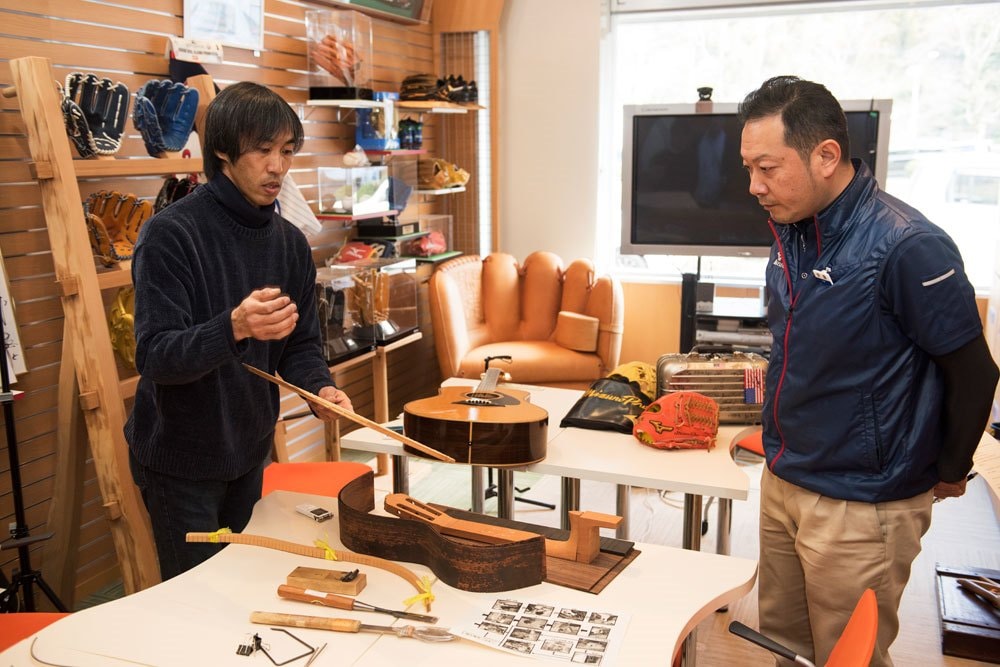
(left) Tadahiro Suzuki of Yamaha (right) Norifumi Ito
“I played baseball myself when I was in junior high, so I've been looking forward to talking with Ito,” said Suzuki. “I had a chance to visit the Mizuno workshop, and I was really excited about the way the craftsmen deal with the glove during each individual process.”
“Glove-making includes many factors, from the selection of leather to the final finishing process,” said Ito. “Each craftsman takes the time to learn every aspect of each process. These cross-trained workers can perform their work with a complete understanding of how each process will affect the glove as a whole.”
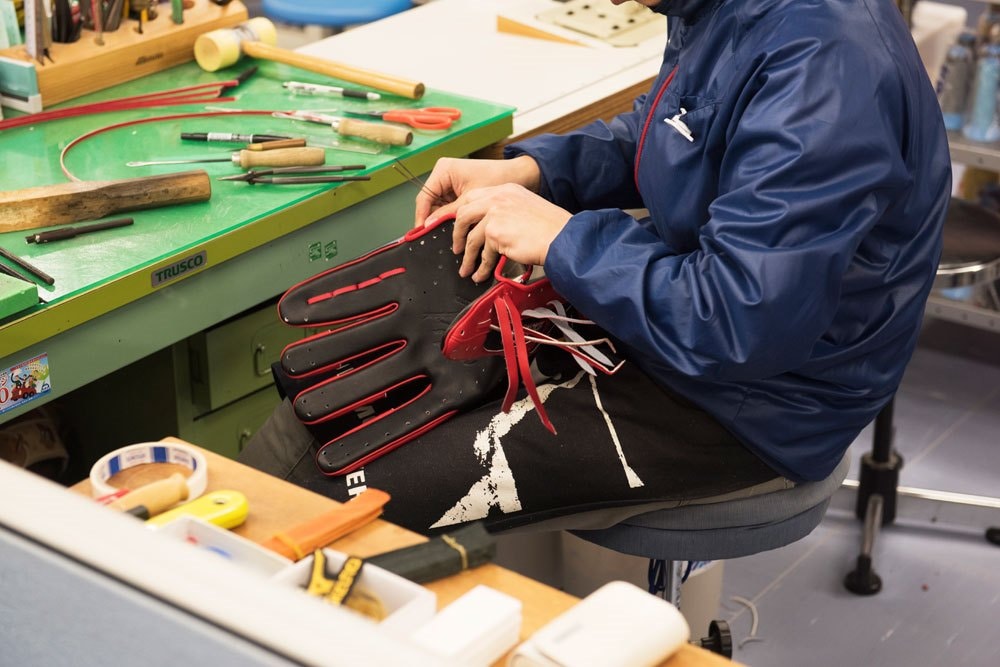
“Guitar making is similarly divided into many pre- and post-processes, and the craftsmen learn all of them but then approach the work step by step,” said Suzuki. “The guitar is simple in structure, but the tone changes greatly depending on the selection and combination of materials and methods. Twenty years in, I’m still exploring new possibilities to produce better sounding guitars every day.”
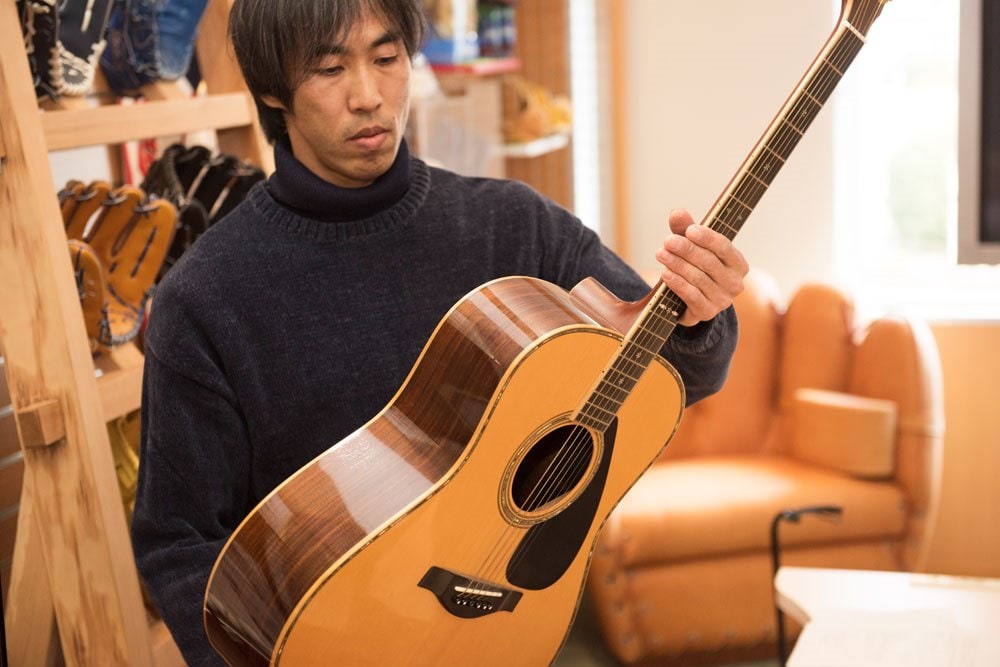
“I started playing baseball in elementary school, and I always knew I wanted to work in baseball,” said Ito. “After being introduced to the world of made-to-order gloves by a teammate, I decided I wanted to make quality baseball gloves by hand. “Today I’m privileged to have been making gloves for Mizuno for more than 26 years.”
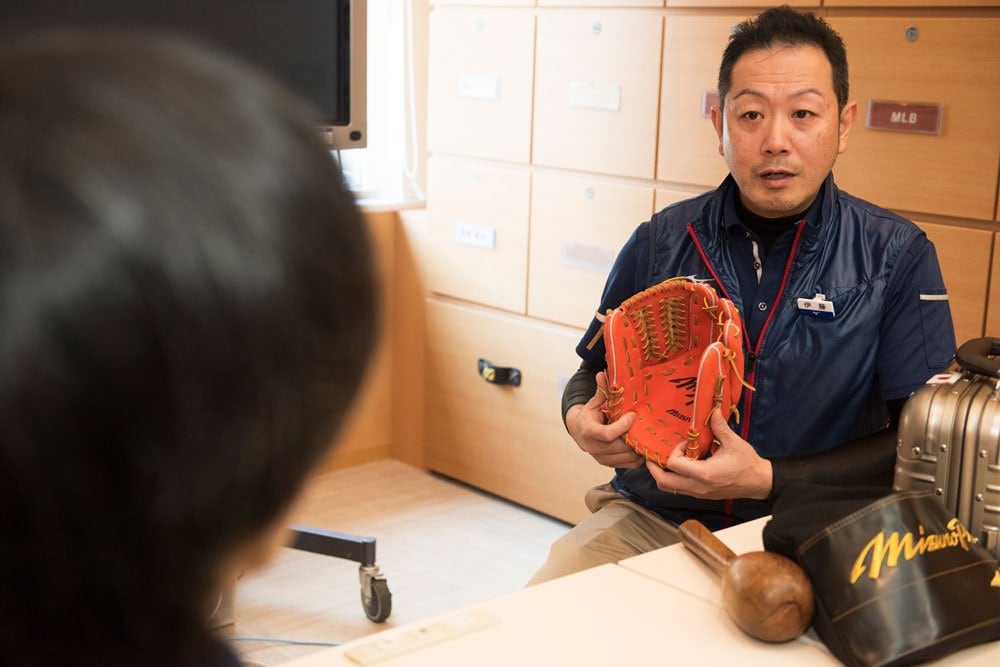
“For me, this job has many rewards,” said Suzuki. “I get to use my own sensibilities to make guitars from scratch, and seeing the final product is very satisfying. When I see a guitar I made with my own hands being used by top musicians on television, it’s amazing to see someone pouring their heart into an instrument I poured my heart into.”
“Seeing someone make an outstanding play with a glove I made makes me happier than anything,” agreed Ito. “You know a Mizuno glove the moment you see it, and catching a sight of that at the ballpark or in the media is my greatest pleasure.”
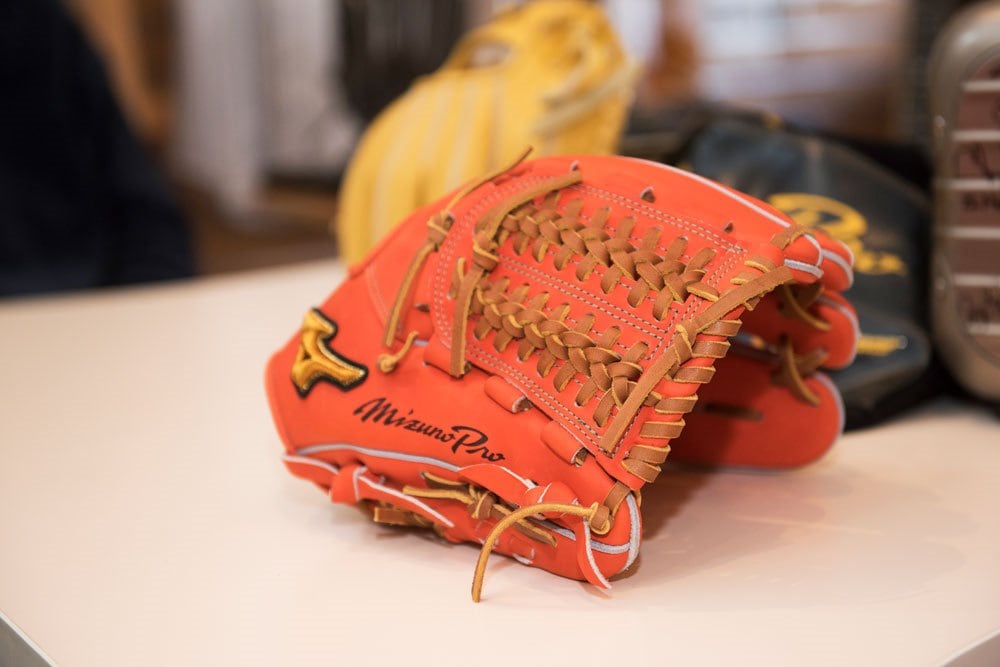
“I always try to put myself in the player’s shoes, and try to fit each glove to the comfort that player is looking for,” continued Ito. “In a sense, I have to challenge my own sensibilities to make a glove that will be cherished by another. I get feedback about the leather’s condition after it’s broken in, and I go through great efforts to adapt to the subtle sensory changes the players ask for.
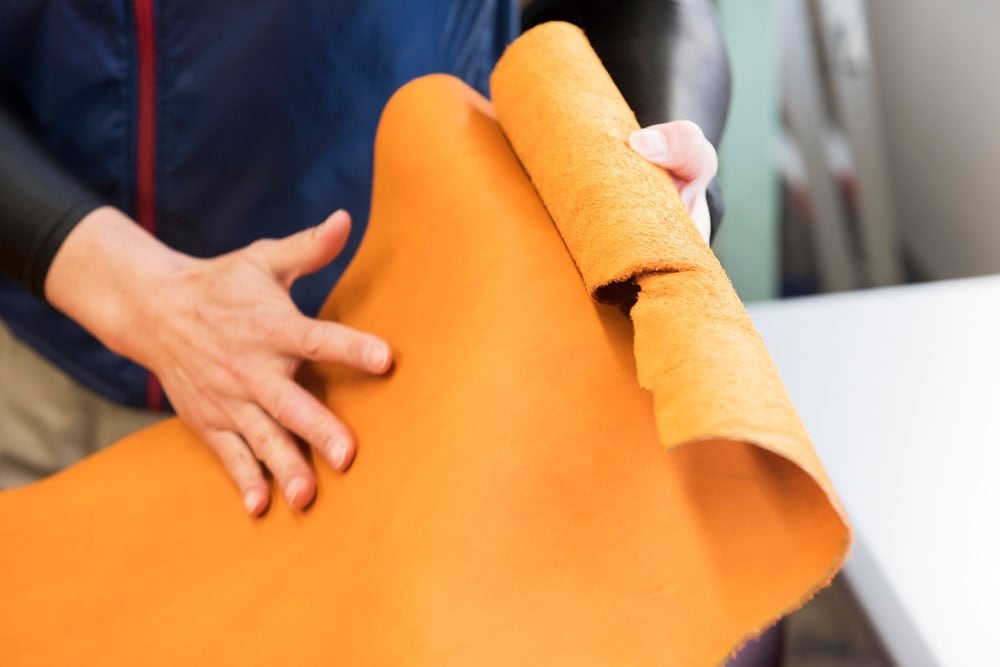
“Knowledge of the materials is a key point in manufacturing,” agreed Suzuki. “With guitars, it’s not enough to have great wood – you have to balance these materials if you want high-quality sound.“
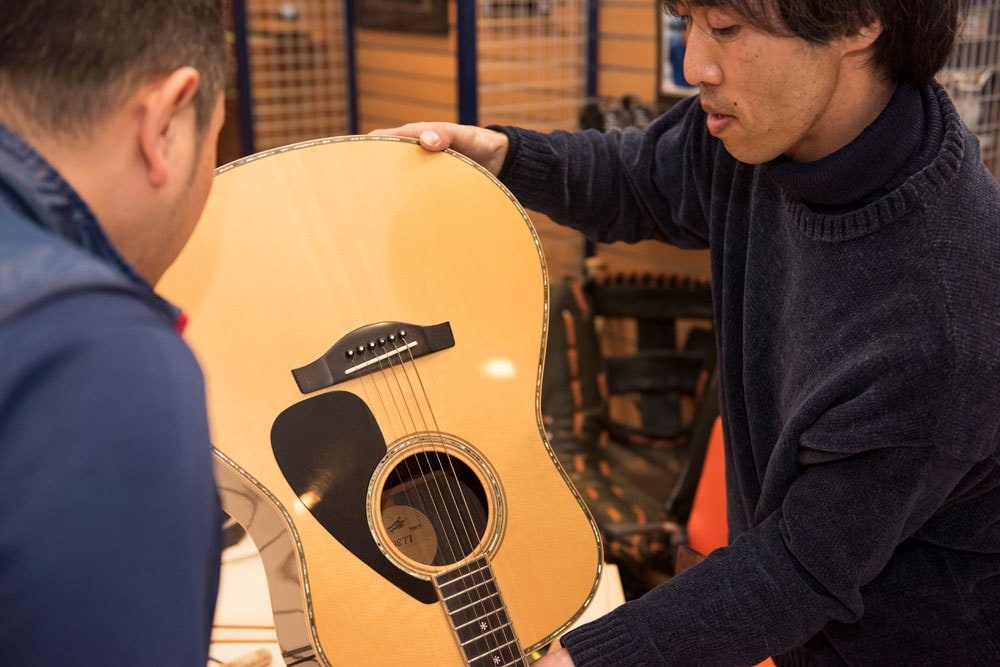
“Just like wood, the texture of natural leather varies widely depending on type and conditions,” related Ito. “I try to preserve each material’s intrinsic qualities and select each piece accordingly to make a well-rounded glove. Today with the need to increase productivity, it’s hard to focus on the techniques of a single process, but some discoveries and improvements are only made through years of repeating the process and learning from watching others.”
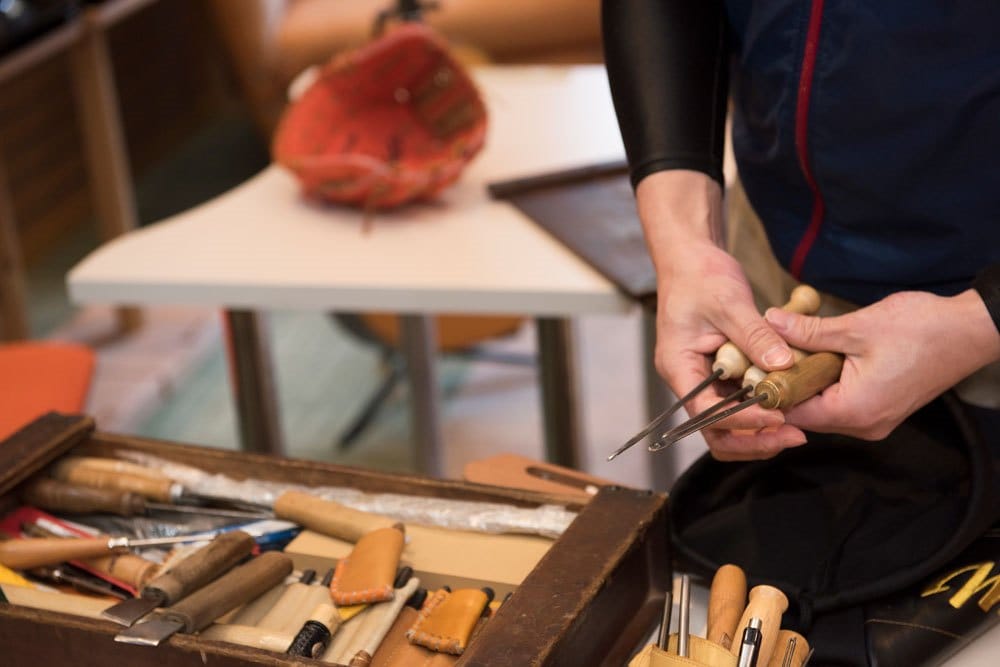
Tools Mr. Ito uses to make gloves
“There are always going to be new discoveries,” remarked Suzuki. “When I compare my work to longtime veterans and even younger assistants, I’m always surprised what I learn from watching others achieve the same results with different techniques.”
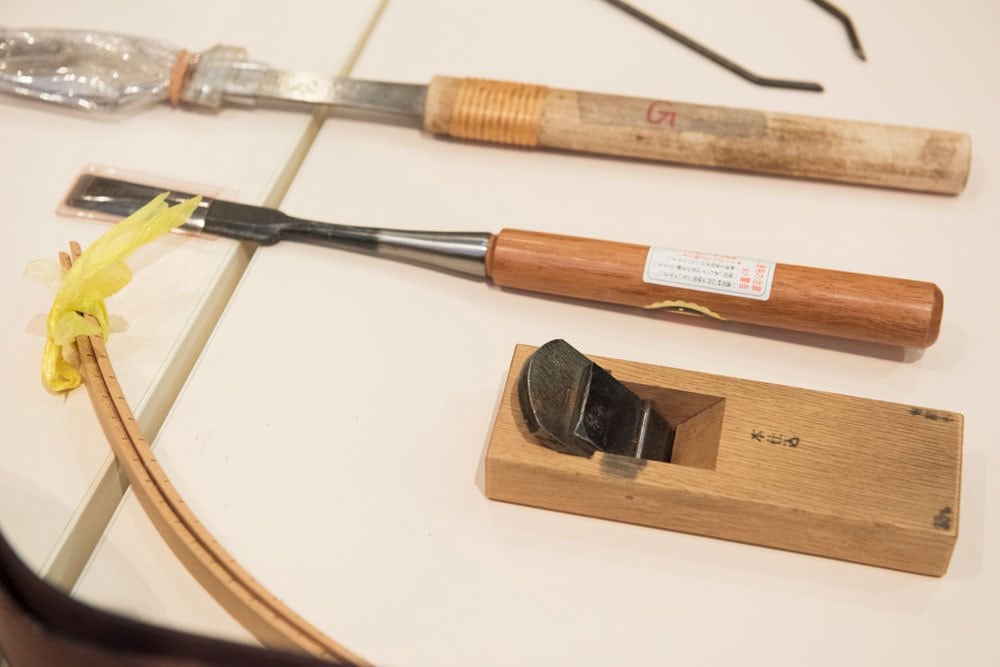
Some of the tools Mr. Suzuki uses to make guitars
“Since no two players are exactly alike, it’s impossible to design the ideal glove,” concluded Ito. “It’s a work in progress, and it takes passion and dedication to work towards always making better products. Until a convincing glove can be created by a 3D printer, we will keep relying on our human senses to provide players with a comfortable and satisfying glove.”
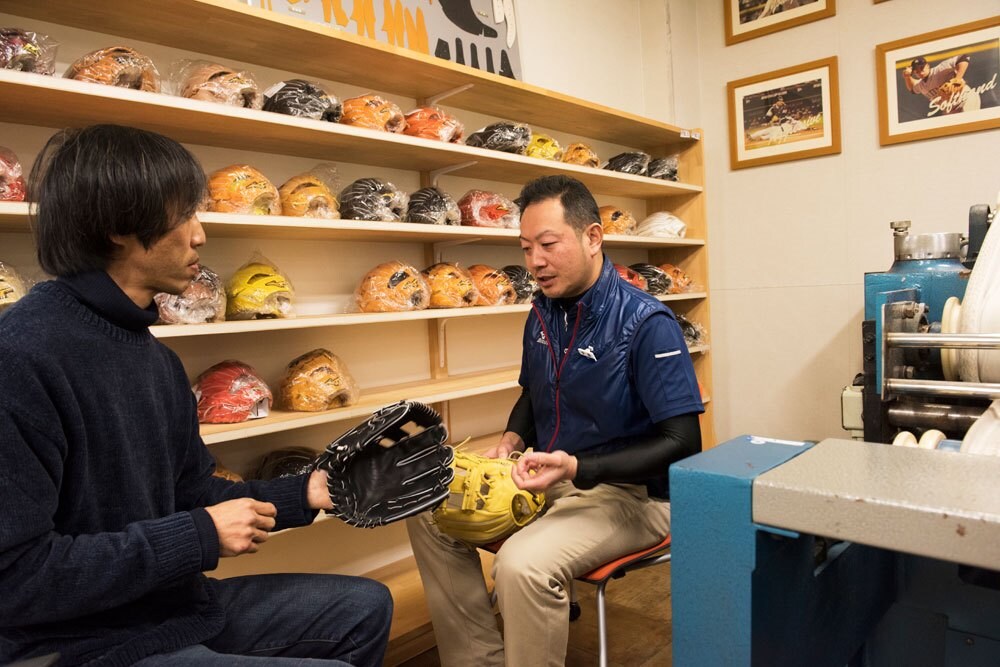
“Technically, you could make a guitar with a 3D printer, but when it comes to producing a guitar that’s satisfying to play, it still takes a human touch,” agreed Suzuki. “There’s a pleasure in always learning how to make your craft better, and I look forward to seeing where we go from here as we continue to sharpen our senses to make the best guitars possible.”
Interview/Text: Fumihisa Miyata, Photos: Naohiro Kurashina