Craftsmanship
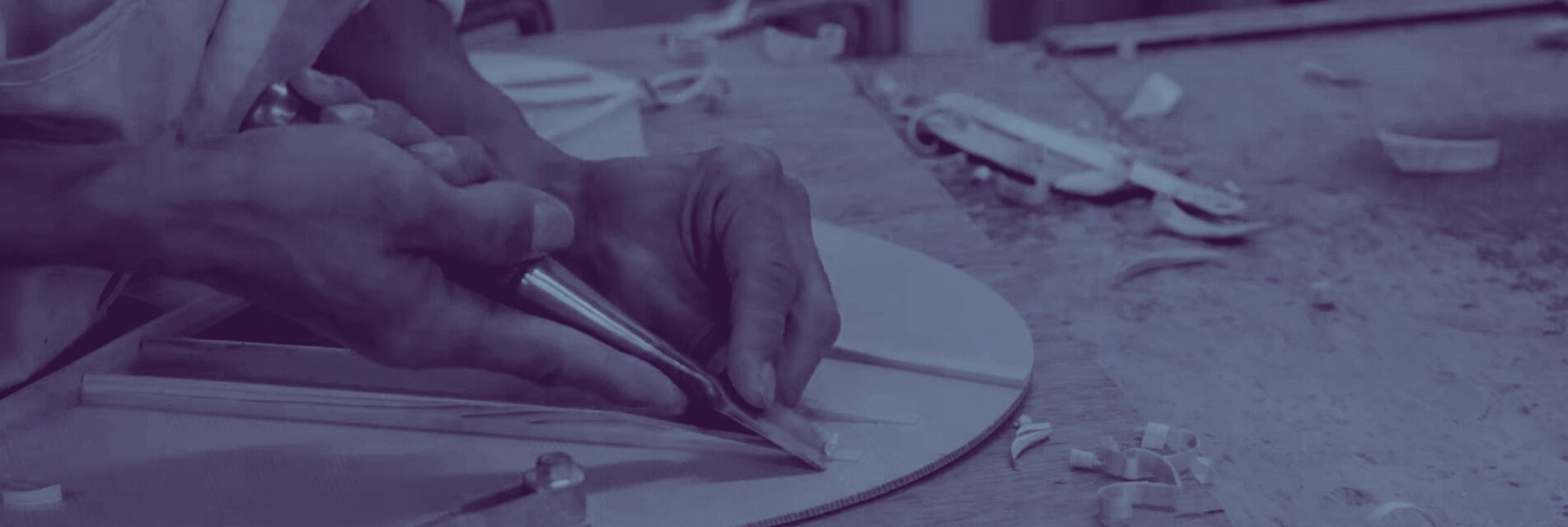
Mesmo com técnicas avançadas de construção, não é possível automatizar a produção de ótimos violões. A complexidade da tarefa, combinada com a necessidade constante de consciência em relação aos materiais usados e a habilidade de ajustar variações sutis, significa que não existe substituto para a habilidade e sensibilidade de um luthier experiente.
Transformando Designs em Ótimos Violões
Transformar designs em ótimos instrumentos não é fácil. Desenhos técnicos não conseguem transmitir o timbre desejado de um instrumento, ou o método de construção necessário para criar o som e as características desejados. Antes da construção de um novo violão começar, os planos e intenções dos designers são discutidos com os luthiers na fábrica para ser desenvolvido um processo de produção apropriado. Cada violão é diferente, e a criação de uma metodologia de produção e workflow ideais para cada violão é crucial.
Exagerando
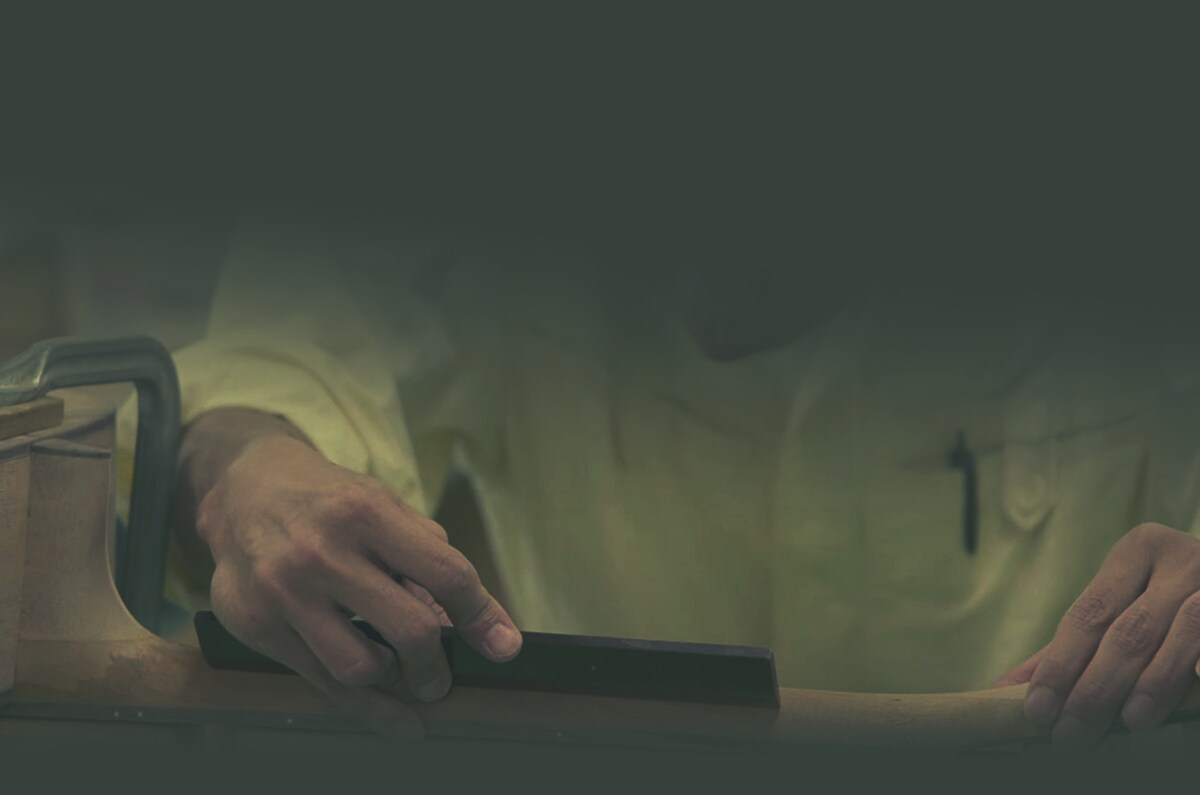
Às vezes "exagerar" nas coisas é a única maneira de assegurar que a qualidade desejada seja atingida com consistência e em toda situação possível. A Yamaha leva os detalhes de produção ao extremo em muitos casos, mas os resultados finais valem a pena. O processo de pré-relação de corpos acústicos e braços da Yamaha antes do acabamento é um exemplo. A experiência nos mostrou que a qualidade da junção do corpo-braço desempenha um papel importante em maximizar o timbre e resposta do instrumento; resumindo, o encaixe precisa ser perfeito com contato íntimo entre o braço e o corpo. O nível de controle e consistência obtidos na construção e acabamento do braço e corpo como pares combinados é um esforço extra que vale a pena.
Mistura Ideal Entre a Precisão da Máquina e a Habilidade Humana
Existem algumas tarefas que são melhores serem deixadas com as máquinas, particularmente aquelas que exigem precisão e repetição extremas; por exemplo, cortar os encaixes dos trastes na escala é um trabalho crucial que é feito por maquinário preciso controlado por computador. Mas para proporcionar instrumentos que atendem verdadeiramente às necessidades do músico, existem elementos que requerem uma atenção e flexibilidade individuais. É onde a habilidade e experiência dos luthiers da Yamaha se destacam.
Os Toques Finais
A Yamaha trabalha duro para assegurar que todos os violões e baixos saiam da fábrica em condições inigualáveis de se tocar. Alguns músicos podem querer realizar pequenos ajustes para atender aos seu estilo individual de tocar, mas os detalhes importantes como nivelamento de trastes e acabamento são elevados aos níveis de instrumentos custom shop dentro da fábrica. A montagem final é uma etapa de fabricação que requer o maior dos cuidados caso se deseje atingir o melhor timbre e desempenho. Partes que não estiverem apropriadamente reguladas ou não firmemente presas podem comprometer tanto o som quanto a tocabilidade, portanto as workstations e processos de montagem são desenhados e configurados para uma montagem suave e eficiente para que o luthier possa se concentrar totalmente em atingir os resultados perfeitos.
Criando as Ferramentas
Muitas das ferramentas utilizadas na fabricação dos violões têm que ser feitas a mão para um propósito específico, e muitas são criadas especificamente para um único modelo e não serão usadas para mais nada. Desenvolver ferramentas e aparatos que facilitam para que os luthiers produzam consistentemente instrumentos perfeitos é um elemento importante do approach da Yamaha quando se trata de construção de violões, mas ferramentas e adereços podem se desgastar e sair do alinhamento conforme o uso, portanto um cuidado especial é tomado para mantê-las revisadas e em condições de trabalho perfeitas sempre: é uma parte escondia mas vital para o controle de qualidade geral.
Mantendo a Produção Viva
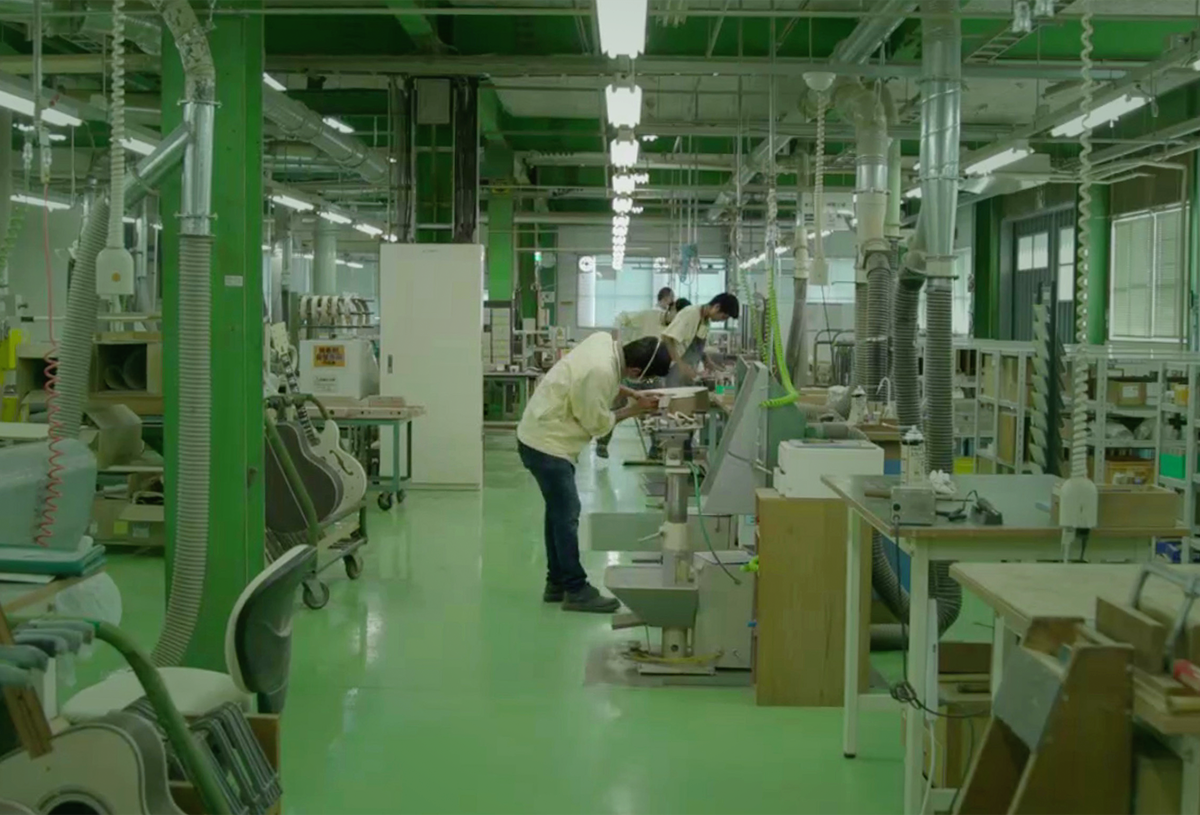
Graças à confiança nos habilidosos luthiers ao fazer ótimos instrumentos, a única maneira de assegurar qualidade contínua e consistente no futuro é passar o know-how para a próxima geração de luthiers. Esse tipo de habilidade só pode ser passada completamente de pessoa para pessoa, entregando ao aprendiz, portanto a Yamaha transforma isso em uma parte oficial do processo de fabricação. O time de fabricantes de violões muda com o tempo, mas a Yamaha está dedicada em assegurar as habilidades básicas, assim como as diversas inovações desenvolvidas através do tempo, sejam passadas adiante para que os violões Yamaha continuem evoluindo.
O processo de fazer violão
PESQUISA E DESENVOLVIMENTO
TRABALHO ARTESANAL
CONTROLE DE QUALIDADE
ANÁLISE ACÚSTICA
ANATOMIA DO VIOLÃO
ANATOMIA DA GUITARRA
MANUTENÇÃO: TROCANDO AS CORDAS